Dependable Welding Inspection Service for Quality Control
Dependable Welding Inspection Service for Quality Control
Blog Article
Discover the Advantages of Different Kinds Of Welding Providers for Your Service

In the realm of industrial operations, the selection of welding solutions plays an essential duty in identifying the high quality and performance of your organization procedures. Each welding method, from MIG to TIG, Arc, and Spot welding, supplies unique benefits that cater to details demands and demands.
MIG Welding Benefits
MIG welding, likewise known as Gas Steel Arc Welding (GMAW), provides countless advantages to businesses seeking reliable and high-grade welding solutions. One key benefit of MIG welding is its versatility in dealing with various kinds of metals, consisting of stainless steel, light weight aluminum, and mild steel. This adaptability makes MIG welding a prominent choice for markets with diverse welding requirements.

Additionally, MIG welding is a cost-efficient choice due to its effective use consumables such as filler material and shielding gas. This efficiency equates to cost savings for services in the lengthy run. On the whole, MIG welding's mix of flexibility, speed, simplicity of use, and cost-effectiveness makes it a recommended selection for many welding applications.
TIG Welding Advantages
Tungsten Inert Gas (TIG) welding provides precise control and extraordinary top quality in welding solutions for companies requiring thorough and high-standard welds - Welding Inspection Service. TIG welding stands out for its ability to produce clean and accurate welds without spatter or stimulates, making it optimal for applications where visual appeals and accuracy are extremely important. One of the key benefits of TIG welding is its adaptability in welding various kinds of steels, consisting of stainless-steel, light weight aluminum, copper, and exotic metals, offering services with an adaptable welding service for various tasks
Moreover, TIG welding makes it possible for welders to deal with thinner products efficiently, as the process permits for lower warm input and better control over the welding arc. This results in very little distortion and a slim heat-affected area, necessary for welding projects where protecting the structural honesty of the base products is important. Furthermore, TIG welding creates top quality, visually appealing welds that usually require very little post-weld cleanup, conserving businesses time and resources. On the whole, the exact control, top quality welds, and versatility make TIG welding a recommended option for services wanting to attain top-notch welding results.
Arc Welding Pros

Area Welding Conveniences
Spot welding uses countless advantages for companies seeking accurate and effective joining of steel parts in their production processes. This welding approach is very affordable because of its quick execution, very little requirement for substantial preparation, and reduced power consumption contrasted to other welding methods (Welding Inspection Service). Area welding likewise provides a clean and neat finish, making it suitable for applications where looks are vital
Among the key benefits of place welding is its ability to create sturdy more information and solid bonds between metal surface areas. The process produces a focused warm source, leading to a localized weld that decreases damage to the surrounding areas. This focused heat application also decreases the risk of bending or distortion in the bonded products, ensuring the integrity of the end product.
Moreover, spot welding is highly versatile and can be made use of on a large array of steels and alloys, consisting of copper, steel, and light weight aluminum. Its flexibility makes it a popular choice for sectors such as vehicle, electronics, and aerospace, where precision and effectiveness are critical. In general, the benefits of area welding make it a useful possession for services looking to improve their manufacturing capabilities.
Welding Solution Option Variables
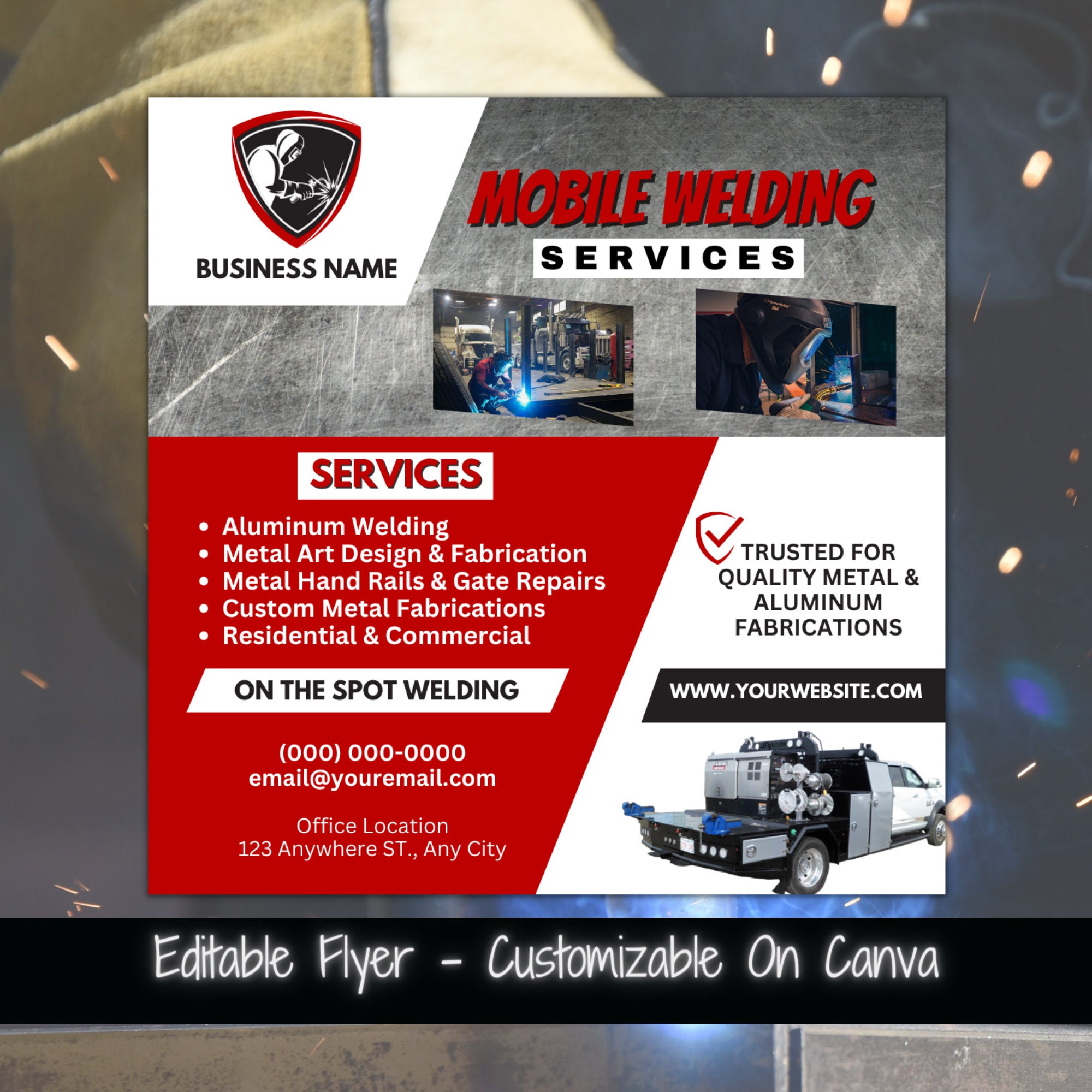
Another aspect to take into consideration is the dimension and intricacy of the elements being welded. Some welding techniques are much better fit for detailed and small tasks, while others are extra effective for bigger and extra straightforward structures. Consider the rate and efficiency of the welding process. Depending upon your production requirements, choosing a welding solution that can fulfill your timeline and result demands is important for preserving performance. Lastly, review the cost-effectiveness of various welding solutions to make sure that you are obtaining the best value for your investment. By thoroughly taking into consideration these aspects, you can select one of the most ideal welding solution for your business requirements.
Conclusion
Finally, recognizing the benefits of various sorts of welding solutions can greatly profit companies in their decision-making process. MIG welding supplies efficiency and rate, TIG welding provides high accuracy and clean welds, arc welding is cost-effective and functional, and place welding is ideal for joining Resources thin products. By thinking about these factors, businesses can choose one of the most suitable welding service to fulfill their details demands and needs.
MIG welding, additionally understood as Gas Metal Arc Welding (GMAW), uses countless advantages to organizations looking for efficient and premium welding solutions. One of the vital benefits of TIG welding is its versatility in welding various types of metals, including stainless steel, light weight aluminum, copper, and unique steels, providing services with an adaptable welding option for different tasks.
Arc welding is recognized for its high welding rate, making it possible for efficient conclusion of welding jobs (Welding Inspection Service). In general, the pros of arc welding make it a useful welding service for organizations looking for a functional, cost-efficient, and reliable welding solution
MIG welding provides efficiency and rate, TIG welding gives high precision and tidy welds, arc welding is versatile and economical, and place welding is excellent for signing up with slim materials.
Report this page